The Continuing Impact of COVID-19 on the Global Supply Chain
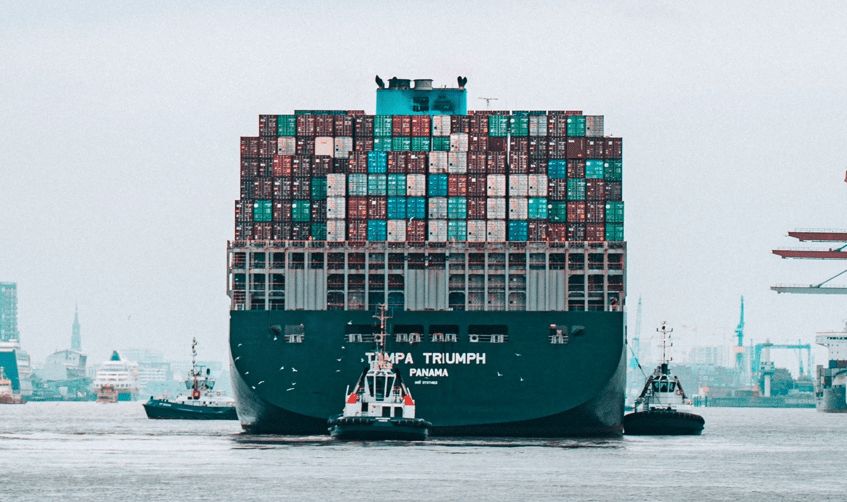
Table of Contents
Over the past two years, global supply chain disruptions have become a pervasive challenge, with the COVID-19 pandemic exacerbating issues like volatile demand, factory shutdowns, and logistical nightmares But which industries were most affected by these stresses to their supply chains? How were companies able to adapt their supply chain management? And what are countries doing to make sure that future shutdowns don’t affect their supply chains so drastically?
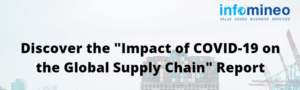
Industries Hit Hardest by Global Supply Chain Disruptions
The COVID-19 pandemic brought to light long-standing vulnerabilities in global supply chains. Lockdowns slowed or stopped the flow of raw materials and disrupted manufacturing in several industries, putting supply chains under significant stress.
Factory shutdowns caused a shortage of semiconductors, already in short supply amid sustained demand from a growing EV market, and the increased demand for electronic goods from consumers confined to homes by lockdowns.
Major automakers bore the brunt of this shortage, made worse by the concentration of the world’s semiconductors manufacturing among just a handful of producers—Taiwan’s Semiconductor Manufacturing Co.(TSMC), for instance, along with South Korea’s Samsung, manufacture a combined 70% of the world’s semiconductor supply.
The automotive industry was also hit hard by the supply chain issues affecting both battery manufacturers, and the mining industry that extracts the rare-earth elements needed for those batteries. Automakers’ over-reliance on the Asia-Pacific region for these critical components was made clear when major battery manufacturers such as BYD and CATL announced extended production delays, forcing automakers to slash production.
The textile and fashion industries are two more to have been extremely hard hit by the global supply chain crisis. With China being a critical global supplier of textile inputs, pandemic-related production disruptions there reverberated throughout the rest of the textile and fashion industries. These industries were further affected when the global transportation system came to a halt, preventing or delaying the transport of components to manufacturers, and finished products to consumers.
Innovative Responses to Supply Chain Challenges
With COVID-19 related shortages exposing vulnerabilities in the global supply chain, companies across different industries have taken action to determine how best to deal with the disruption and mitigate the effects of future supply chain shocks.
China plus one strategy
One way to address the risks associated with over-reliance on a single supply source, is to use sources in locations not vulnerable to the same risks. This is the core idea behind the ‘China plus one’ strategy currently in use by several major companies. It emphasizes diversification by establishing a factory in one other developing Southeast Asian country – such as Thailand or Vietnam – in addition to existing facilities in China, to minimize the risks of geographic concentration.
Strengthening local supply networks
Some companies are strengthening their supply networks by investing in local suppliers. Samsung, for instance, has invested a combined $238 million in nine midsize companies since the summer of 2020, to develop a network of chip equipment and materials suppliers inside South Korea and reduce its reliance on overseas suppliers. Similarly, Tesla is creating a domestic US lithium supply chain by sourcing the lithium ore necessary for lithium-battery fabrication within the US, thereby reducing its reliance on traditional lithium-producing countries.
Innovative workarounds
Major companies have been forced to find innovative solutions to their supply chain problems. Tesla, for instance, has dealt with the chip shortage by rewriting vehicles’ software to support alternative chips.
Cardinal Health, a leading US healthcare services company, has turned to the use of tracking software to track shipments of their products between manufacturing plants and Cardinal’s distribution centers. This allows for the making of predictive decisions to adjust supply plans and production schedules.
How are countries making sure that future shutdowns don’t affect their supply chain?
Global supply chain problems have made clear to governments the need to take action to strengthen and support their domestic supply chains, and many have taken important first steps towards doing just that, in preparation for future crises.
USA
President Biden signed an executive order in February 2021, for a comprehensive review of critical US supply chains, with the associated White House report being released in June. Among other recommendations, the review determined that a solid supply chain must include a small and medium-sized business manufacturing base and highlighted the US’s need to diversify its international suppliers to reduce the risks associated with geographic concentration.
Japan
The Japanese government has focused its efforts on subsidizing local businesses to strengthen domestic supply chains. It has distributed 146 subsidies totaling 247.8 billion yen ($2.4 billion) with the goal of encouraging an increase in domestic manufacturing, to reduce the country’s dependence on Chinese supply. Japan is also investing in overseas rare earth minerals projects, particularly in Australia and India to reduce its reliance on China’s supply from 58% registered in 2019, down to 50% by 2025.
Outlook: The Global Supply Chain Looking Forward
As lockdowns have lifted and a global economic recovery has gathered pace, consumer demand has increased sharply. Supply chains that were disrupted during the crisis continue to face significant challenges and are struggling to bounce back, much less meet increased demand. While companies and governments alike have taken substantial action in response to the supply chain crises, these will not be sufficient to solve supply chain woes in the near term. Months of shipping backlogs and continuing labor shortages have caused bottlenecks that are proving difficult to resolve, and most analysts agree that supply chain problems will only get worse before they get better, with some estimates warning that the crisis could last another two years.
Author: Mohamed SAIDI
Sources
https://www.ey.com/en_gl/supply-chain/how-covid-19-impacted-supply-chains-and-what-comes-next
https://www.pwc.com/ng/en/assets/pdf/impact-of-covid19-the-supply-chain-industry.pdf
https://hbr.org/2020/09/global-supply-chains-in-a-post-pandemic-world
https://www.nytimes.com/2021/10/02/business/tesla-electric-q3-sales.html
https://www.theverge.com/2021/7/26/22595060/tesla-chip-shortage-software-rewriting-ev-processor
https://techwireasia.com/2021/10/heres-what-the-2021-global-semiconductor-shortage-is-all-about/
https://www.argusmedia.com/en/news/2191594-qa-chip-shortage-shows-need-to-diversify-supply-chain
https://www.eenewsanalog.com/news/reports-tsmc-lost-market-share-2q20
https://www.e3s-conferences.org/articles/e3sconf/pdf/2021/21/e3sconf_aeecs2021_03044.pdf